
Industrial robots, semiconductor manufacturing equipment, CNC machine tools, metal processing machines, and other equipment and devices in factories are manufactured based on an centered operation system from a controller as a brain called a programmable logic controller (PLC). Each device’s data is given a work ID, time stamp, and other information. However, this production system makes it difficult to determine the reason why the equipment stopped. Because when something is wrong with the device, an instruction layer receives only the result either if it works or not.
A newly developed YRM-X controller captures both operation data and results from the motion of the motors of each device, so that it can be used to determine when, with which device, and how it was processed, thereby enhancing traceability until product completion. In addition, real-time data on the same time frame, such as quality data, can be obtained when a device is connected, so that in the event of a device failure, the cause of the problem can be determined accurately.
Other solutions
-
Production
-
Quality
-
Maintenance
Flexible production
Accuracy improvement
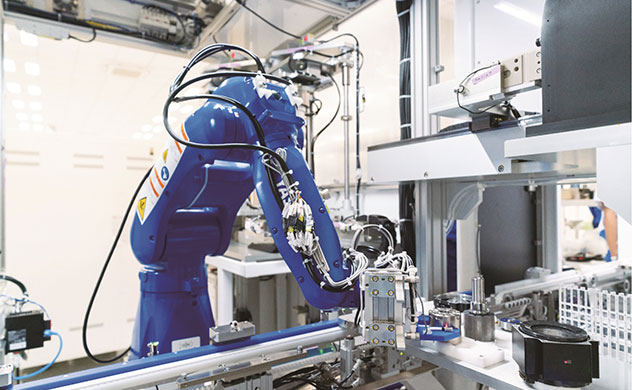
Accuracy Improvement of Defect Cause Analysis < Yaskawa Case >
By “visualizing” the operation status of equipment/devices with Yaskawa Cockpit, it is possible to identify the root cause by comparing the normal value and abnormal value of the data in the factor analysis for defects in production.
Quality inspection
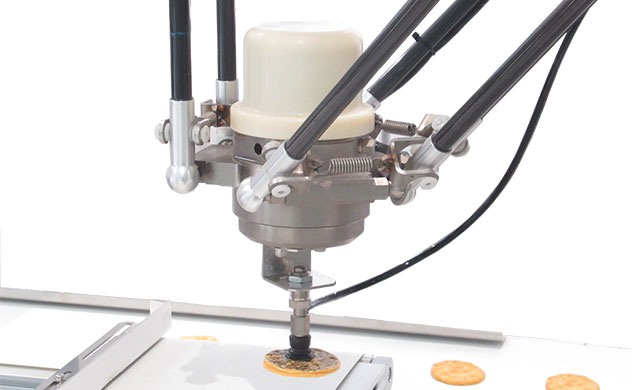
Automated Product Quality Assessment with AI
When the quality inspection process is labor-saving, the use of an image judgement service that utilizes AI technology such as deep learning makes it possible to automatically determine complex No Good patterns with the same level of accuracy as humans.