
Our unique planning technology virtually simulates the optimal path of multiple robots. For example, when a spot welding robot for an automobile body suddenly stops during operation in a process where 8 to 10 robots are placed close to each other, it may then be necessary to return the robot to a zero position. Regarding which robot arm can be moved first to return to the origin without bumping into other arms, it takes many hours even for a skilled worker to operate it with a programming pendant. However, by automatically generating the optimal path with the planning function, the simulation can be completed in a few minutes, greatly reducing engineering time for recovery.
This technology can also be applied to automatic path generation when field conditions are uncertain, such as picking of randomly placed objects.
Other solutions
-
Production
-
Quality
-
Maintenance
Flexible production
Accuracy improvement
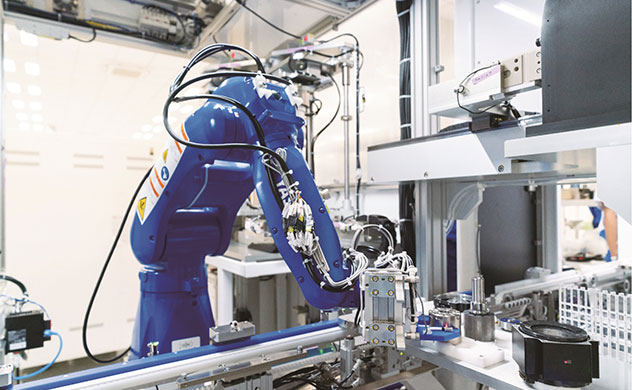
Accuracy Improvement of Defect Cause Analysis < Yaskawa Case >
By “visualizing” the operation status of equipment/devices with Yaskawa Cockpit, it is possible to identify the root cause by comparing the normal value and abnormal value of the data in the factor analysis for defects in production.
Quality inspection
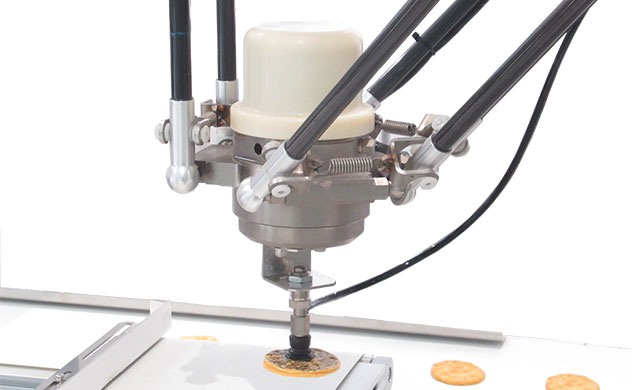
Automated Product Quality Assessment with AI
When the quality inspection process is labor-saving, the use of an image judgement service that utilizes AI technology such as deep learning makes it possible to automatically determine complex No Good patterns with the same level of accuracy as humans.